Уже сейчас, на ранних стадиях разработки, пленка из нового материала по прочности не уступает алюминиевой фольге, однако растянута может быть на 25 процентов сверх своего размера. Алюминиевая фольга рвется при 2-процентном растяжении.
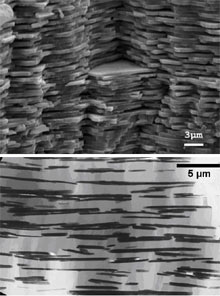
Кроме того, материал очень легок: сталь аналогичной прочности весит в два, а то и в четыре раза больше. Секрет подобной прочности наряду с эластичностью и легкостью — в мельчаших пластинках оксида алюминия, слоями рассеянных в биополимере. Процесс производства состоит в том, что пластинки охида алюминия размешиваются в этаноле, а смесь распределяется по поверхности воды. Затем в воду погружают стеклянную пластину, чтобы пластинки осели на ней. Наконец, поверх этого слоя наносят биосовместимый полимер хитозан. Процесс повторяют много раз, покуда толщина композита не достигнет нескольких десятков микрометров, после чего материал снимают острым лезвием.
Вдохновением для исследователей послужила механическая структура перламутра, блестящего покрытия внутренней поверхности морских раковин. Пластинки в перламутре состоят из карбоната кальция, а основным материалом служит полимер на белковой основе (см. фото: на верхнем снимке структура перламутра, на нижнем срез нового нанокомпозитного материала). Важнейшим параметром оказалось соотношение между длиной и толщиной пластинок. Если оно слишком высокое, то пластинки ломаются при натяжении материала; если слишком низкое, материал становится недостаточно жестким.
Оксид аллюминия, выбранный учеными в качестве материала для пластинок, в пять раз прочнее карбоната кальция в перламутре. Чтобы избежать возможных изъянов в структуре пластинок, их толщину уменьшили до 300 нанометров по сравнению с 500–1000 нанометров у природных бляшек. Оптимальным средним отношением длины к толщине оказалось 40, поэтому длина пластинок — 5–10 микрометров.
Потенциальная область применения нового материала широка: это и более долговечные костные и зубные имплантаты, и более легкие детали для автомобилей и самолетов, позволяющие экономить больше топлива, и электронные приборы, которые можно будет делать гибкими и прозрачными. Например, стекловолокно, применяемое сейчас в автомобилестроении, выдерживает нагрузку только в одном направлении, перпендикулярном направлению усиливающих его волокон, новый же композит прочен в двух направлениях, благодаря рассеянным в нем пластинкам.